Understanding Quickshifters and Slipper Clutches
Forget about brushing up on your cornering skills. If you really want to go fast then focus on changing up and down the gears swiftly and cleanly
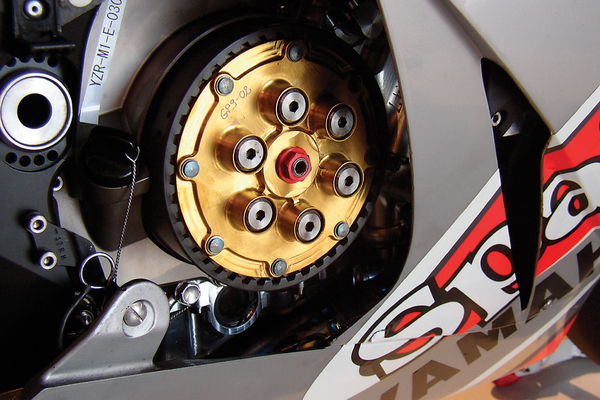
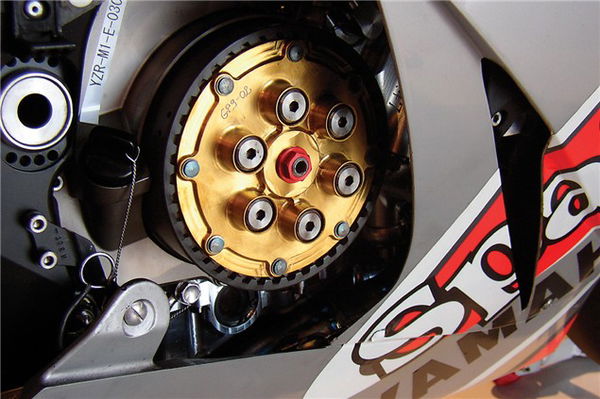
Before we go further, it's important to grasp how a motorcycle's 'drivetrain' (engine and gearbox) works. Very early machines worked on direct drive - ie the engine was directly connected to the rear wheel - so you had to switch off the engine when you hit a junction or to change gear. But then came the clutch - a mechanism that separates the running engine from the rear wheel. The clutch transmits power from the engine to the rear wheel via the gearbox, giving the rider control over the connection between crankshaft and transmission. Use the clutch lever to disengage the clutch and the engine will run freely without turning the rear wheel; disconnect the drive and, by removing the load from the gearbox, the clutch will also allow different gear ratios to be selected.
So how does a clutch work? Imagine a circular friction plate connected to the crankshaft, and a steel plate connected to the gearbox shaft. The friction plate rotates with the crankshaft and as it's pushed against the steel plate, the friction plate turns the steel plate, thus transfering drive from the engine to the gearbox shaft. Slacken off the pressure between the two plates to create a slight gap and 'slip' will occur so the engine will run freely without rotating the gearbox shaft.
Clutch springs push the plates together to transmit drive, and as you pull the clutch lever in you slacken the pressure from the springs, causing the clutch to 'slip'. The gearbox shaft is connected to the rear wheel via a drive mechanism, usually chain or belt.
Rather than using one gearbox plate and one crankshaft plate, modern bikes get multiple plates enclosed in a casing where the gearshaft's steel plates are sandwiched between the crankshaft's friction plates - with the plates either running in oil (wet clutch) or er, not (dry clutch). Reckon it's weird that a mechanism ruled by friction runs in oil? Well, oil cools the plates and lubricates bushes and bearings, as well as quietening that rattling noise which punters might find disconcerting on a production bike. Race bikes usually run with dry clutches as they tend to be more compact: because a wet clutch does not produce as much friction, it needs to be larger or contain more plates.
Problem is, by the time the rider has pulled in the clutch, rolled off the throttle, changed gear and rolled the throttle back on not only a fuel injected bike will they have lost time but the bike will pitch and dive, upsetting handling, suspension and geometry. Even clutchless change-ups take on average 300 milliseconds for a skilled rider to perform - yep, that's a lot.
Enter quickshifters. These gadgets kill the engine momentarily, taking the load off the gearbox to let you shift up the gears without backing off the throttle. The secret lies in interrupting the engine faster than is humanly possible to operate the throttle so time spent shifting gear plummets typically to between 15 and 50 milliseconds - that's quick. As well as saving time (see chart below), it won't unsettle the suspension and the bike will be more stable, especially in a corner. Oh, and a constant throttle is also more fuel efficient, albeit marginally!
The quickshifter comprises a mecanical sensor that triggers an electronic interrupt device to the bike's ignition. On a bike fitted with old-style carbs, this box is hardwired into the ignition coil wires to interrupt the ignition's electrical supply, while on the device interrupts the ignition via the wiring harness at the ECU. Translogic has developed a system for fuel injected bikes that interrupts the signal from the ECU to the injector (hence cutting the fuel supply, see Fuel's Gold, September issue), again via the wiring harness at the ECU.
The mecanical sensor also varies. It is either positional - ie you adjust it to the positioning of the gear lever, and as the lever's position moves it sends a trigger to the electronic interrupt box. Or it's a pressure sensor - ie shifting the lever without shutting the throttle puts pressure on the gearbox, and a pre-determined amount of pressure triggers the control box. A positional system tends to fall out of adjustment and if you need to replace the gear lever at the track (ie after a crash) you have to re-adjust the entire system, hence GP and WSB teams opt for the pressure trigger: it's more convenient to install and is less likely to fall out of adjustment, but it puts pressure on the gearbox and because it works with greater tolerances, it isn't as consistent.