D.I.Y: Gas flow into the cylinder
If an engine is going to make power it needs fuel to do it, and fast and efficient gas flow into the cylinder is critical. How is it done, and how can it be improved?
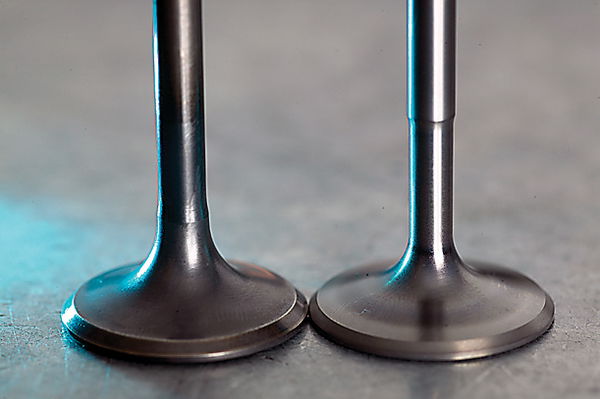
An inlet port's job isn't very difficult. All it has to do is allow the passage of the fuel/air mix from the carbs or fuel injectors at one end to the inlet valve at the other, through which it passes on into the cylinder.
In order to do this as smoothly and efficiently as possible, inlet ports need to be as straight and obstacle-free as the design of the engine and chassis allows. It also helps if they err to the vertical, as gravity can be used to give an added boost to the fuel/air mix on its journey into the cylinder. Look at the cutaway shot of the ZX-6R on page 22. The inlet port is straight and true, slanting downward at an angle of around 70°.
These days, on the whole, standard cylinder heads work pretty well. They're well made, well designed and flow gas pretty well for motors in a standard state of tune. But the limitations of mass production mean there are compromises in the design, particularly in the port shape and, in some cases, the surface finish.
"Every engine's different," says FW Development's Frank Wrathall. "Some come with good inlets, some come with good exhaust ports, but there are some surprises. For example, when we looked at the
GSX-R1000's ports and valves we didn't think it would make as much power as it does, but it's been a tremendous success."
If you're looking to get more power out of a motor, the first step is to fit a free-flowing exhaust and adjust the fuelling to suit. After that, the next stage is to have the cylinder head 'gas flowed' - in other words, reprofile the inlet and exhaust ports in the cylinder head to allow the fuel/air mix to flow in and exhaust gases flow out more efficiently.
One thing you can't get away from is having the valve stems poking through the ports and interrupting gas flow. These days valve stems come about as thin as it's possible to get away with, but 'waisting' the stem was once common tuning practice - in other words thinning the stem where it protrudes into the port by as much as was safely possible. Removing material from the valve guide where it protrudes into the port and interrupts gas flow can also help.
Big ports obviously flow more gas, but simply widening the inlet tract as far as the cylinder head allows isn't the answer. In fact, narrowing the standard inlet port can reap benefits. An FW Developments supersport-spec CBR600RR actually has narrower inlet ports with a different shape to standard, with material added to the cylinder head which is then ground away and reshaped to the desired dimensions.
However, while supersport tuning rules allow the porting and polishing of cylinder heads, the addition of material by welding is outlawed - you can't stick blobs of metal in your ports and grind it back. For race use FW get round this by reprofiling the ports with Loctite 3475 epoxy putty, which is tough enough to withstand life in a racing engine. Don't try this at home, though.
So why doesn't the CBR come with the port shape FW Developments work towards? "It's easier to cast a round hole than one this shape," explains FW's Ian Park. Although, for 2005, Honda have decided it 's worth the effort.
But why restrict the port at all? If the gas flow is restricted by forcing it through a narrower port, it creates a venturi effect and increases the gas's velocity. It's like putting your thumb over the end of a hosepipe to get the water to spray further - you're not increasing the water pressure but, by reducing the aperture through which it flows, its velocity increases.
This is useful when it comes to getting fuel/air into an engine, because the faster we can get the incoming gas to travel, the more we can squeeze into the cylinder in the very limited time the intake valve is open. And the more we can get in, the more power the engine will make.
A high velocity gas flow has other advantages. One problem encountered with a relatively slow-moving gas charge is poor atomisation and 'drop out', where droplets of fuel actually fall out of suspension. To burn effectively, the incoming fuel/air has to be well mixed as it enters the combustion chamber. If it isn't, or if fuel is dropping out of suspension in the inlet tract and not finding its way into the cylinder at the right time or with the right amount of air, then combustion - and power - will be affected.
But port design has to be a balance between maintaining the fuel/air's velocity at low and mid-range rpm, while not restricting its flow at high revs. The higher an engine can safely rev, the more horsepower it will make, but the upper rpm limit will be restricted by gas flow into the cylinder. It's all very well having an engine that can safely rev to, say, 20,000rpm (ie, do so with out exploding), but if the port volume and valve timing won't allow enough gas into the cylinder during the intake cycle, the engine won't make power.